The Biggest Fleet Repair Mistakes Business Owners Make
Discover the biggest fleet repair mistakes business owners make and how to avoid costly downtime. Learn best practices for fleet maintenance in Edmonton, AB.

Managing a fleet comes with a unique set of challenges. Keeping trucks on the road while controlling repair costs and maintaining compliance requires careful planning and attention to detail. However, many fleet owners fall into common pitfalls that lead to unexpected breakdowns, costly downtime, and regulatory fines. Avoiding these fleet repair mistakes can save your business thousands of dollars and keep operations running smoothly.
Neglecting Preventive Maintenance
One of the most costly mistakes fleet owners make is failing to prioritize preventive maintenance. Waiting until something breaks to fix it may seem like a way to cut costs, but it often results in higher repair bills and longer downtime. Regular maintenance helps identify wear and tear before it becomes a problem. Fleet managers don’t have to worry about unplanned breakdowns missed deliveries and lost revenue.
It’s best to implement a scheduled maintenance plan based on mileage and operating conditions. Some ways to do this are to work with a repair shop to plan it or use fleet management software to track maintenance intervals. It’s also best to train drivers to conduct thorough pre-trip inspections.
Relying Solely on In-House Repairs
While having an in-house repair team can be cost-effective for minor repairs, relying solely on them for major issues can be a mistake. In-house teams may lack specialized knowledge, tools, or access to the latest diagnostic technology.
Why it's a mistake:
- Complex repairs require specialized skills that in-house teams may not have.
- Delayed repairs due to limited parts availability can affect operations.
- Poor diagnostics can result in recurring issues.
How to avoid it:
- Partner with a trusted heavy-duty repair shop for complex repairs.
- Invest in training and tools to enhance your in-house team’s capabilities.
- Develop relationships with local service providers to expedite repairs.
Ignoring Driver Feedback
Drivers are the first line of defense when it comes to identifying vehicle issues. Many business owners dismiss driver feedback, assuming that minor complaints can wait until the next scheduled service. This oversight can result in major mechanical failures down the road. Drivers spend the most time in the vehicle and can detect early warning signs. Leaving these concerns unaddressed means unsafe driving conditions.
You should create an environment that lets drivers speak their minds. Encourage an open feedback culture where drivers report any performance irregularities. You can implement a simple system for drivers to log maintenance concerns. With these in place, it becomes easy to address reported issues to prevent escalation.
Using Cheap Parts and Fluids
Cutting corners with cheap replacement parts and low-quality fluids might save money upfront, but they can lead to expensive repairs and reliability issues in the long run. Inferior parts often wear out faster, leading to more frequent breakdowns and performance issues.
Why shouldn’t you use low quality parts & fluids:
- Low-quality parts fail more frequently, leading to additional repair costs.
- Incompatible fluids can damage critical components like engines and transmissions.
- Cheap filters and oils can reduce fuel efficiency and engine lifespan.
- High-quality components and fluids will last much longer.
What you should opt for:
- Use OEM (Original Equipment Manufacturer) or high-quality aftermarket parts.
- Follow manufacturer recommendations for fluids and lubricants.
- Work with reputable suppliers to ensure product quality.
Delaying Tire Replacements
Tires are one of the most critical components of fleet safety and efficiency. Worn-out tires compromise traction, fuel economy, and driver safety. Many fleet owners delay tire replacements to cut costs, which can lead to blowouts and costly roadside repairs.
Reasons to upkeep your tires:
- Bald or underinflated tires increase stopping distances and accident risks.
- Poor tire maintenance leads to higher fuel consumption.
- Tire blowouts can cause expensive damage to the vehicle and cargo.
- Quality tires will increase revenue as you burn less fuel and reduce wear.
How to avoid it:
- Regularly inspect tires for tread wear, sidewall damage, and pressure.
- Rotate tires based on manufacturer recommendations to ensure even wear.
- Invest in fuel-efficient tires to improve performance and longevity.
Overlooking Compliance Requirements
In Edmonton, AB, fleet owners must comply with provincial and federal regulations, including CVIP standards and safety mandates. Failing to stay compliant can result in hefty fines, increased insurance premiums, and potential business shutdowns.
Why it's a mistake:
- Non-compliance can lead to vehicles being placed out of service.
- Regulatory violations can damage your company's reputation.
- Safety audits may uncover avoidable issues, leading to costly penalties.
How to avoid it:
- Keep up to date with Alberta Transportation regulations and CVIP requirements.
- Schedule regular compliance checks to ensure readiness.
- Maintain detailed service and inspection records for each vehicle.
Underestimating the Importance of Record-Keeping
Accurate maintenance records are essential for compliance, resale value, and warranty claims. Poor record-keeping can lead to missed service intervals and challenges when selling or leasing fleet vehicles. Incomplete records can make it difficult to prove compliance. And poor documentation can lower resale values. Warranty claims may also be denied without proper service history.
It’s best to use digital fleet management systems to track all repairs and inspections. You should keep organized maintenance logs for each vehicle. Regularly auditing records will ensure completeness and accuracy.
Protect Your Business by Fixing These Errors
Avoiding these common fleet repair mistakes can help fleet owners, reduce costs, improve safety, and extend the lifespan of their vehicles. Prioritizing preventive maintenance, driver feedback, and high-quality parts can make all the difference in keeping your fleet running efficiently.
At Fleetgo Heavy Duty Inc., we help businesses stay ahead of fleet maintenance challenges by offering expert repair and maintenance solutions tailored to your operational needs. Contact us today to schedule your fleet inspection and ensure your trucks are road-ready year-round! To learn more about heavy-duty trucks, read our article on five fleet services that improve performance.
More Articles
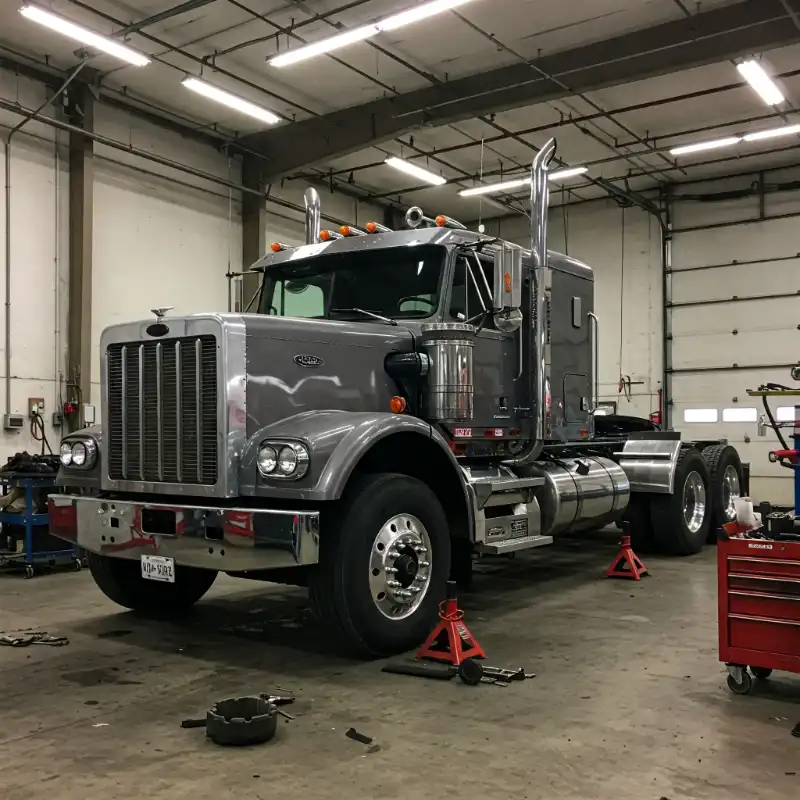
5 Common Issues Found During CVIP Inspections in Edmonton
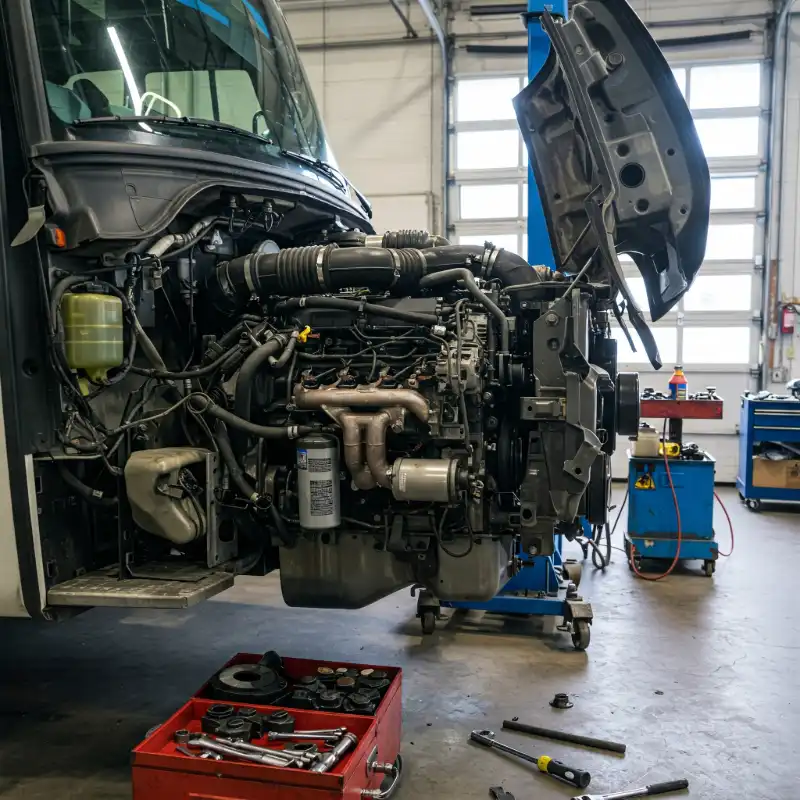
Spring Driving Prep: What Your Car Needs After Winter

Tips For Building A Strong Partnership With A Heavy-duty Truck Fleet Repair Shop
Contact FleetGo
Get in touch with Fleetgo today to request a quote or to schedule in-shop or mobile services in Edmonton & the surrounding area! Our mobile service extends to a 100km radius around Edmonton for emergency roadside assistance & mobile truck & fleet repairs, including Sherwood Park, Spruce Grove, Fort Saskatchewan, St. Albert, Stony Plain, along Highway 16, & more!
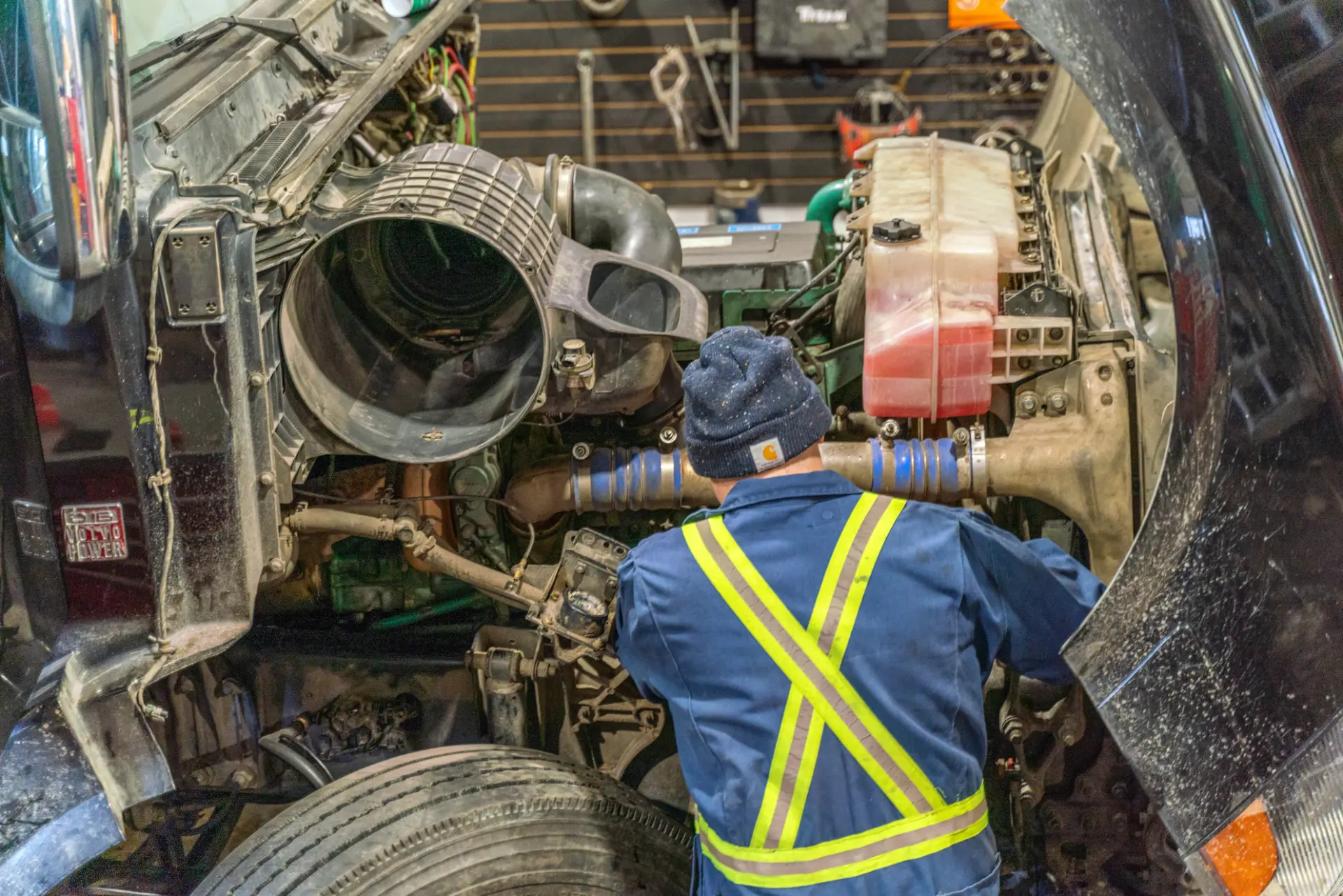