Tips For Building A Strong Partnership With A Heavy-duty Truck Fleet Repair Shop
Discover how to build a strong partnership with a heavy-duty truck fleet repair shop. Learn tips on trust, communication, and preventative maintenance for fleet success.
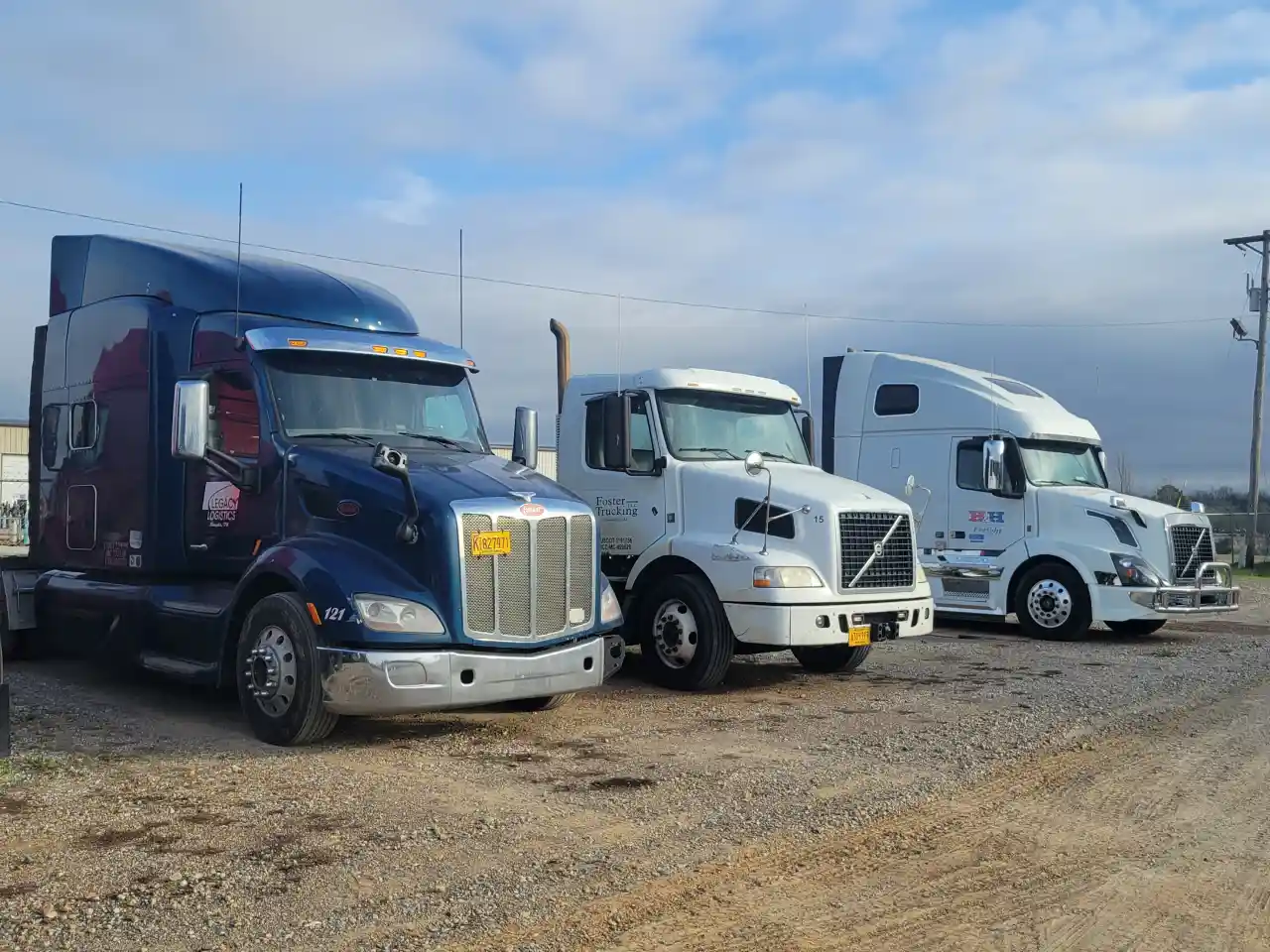
Tips For Building A Strong Partnership With A Heavy-duty Truck Fleet Repair Shop
Managing a heavy-duty truck fleet involves more than just vehicles; it’s about maintaining uptime, ensuring safety, and optimizing costs. A key part of achieving these goals lies in the partnership you build with a reliable repair shop. Such a partnership can mean the difference between smooth operations and constant headaches. To create a robust relationship, you need a strategic approach that blends communication, trust, and foresight. Let’s dive into actionable ways to strengthen this critical connection.
Communicate Clearly and Frequently
In any partnership, communication reigns supreme, and this is especially true for fleet managers and repair shops. Miscommunication can lead to unnecessary downtime, inflated repair costs, or even compliance failures. To avoid these pitfalls, prioritize open and consistent communication.
Implement a fleet management software that both you and your repair shop can access. Shared visibility into maintenance schedules, repair progress, and costs can reduce miscommunication and improve overall efficiency.
- Define Expectations: Make sure both parties understand the required service standards, repair timelines, and reporting formats.
- Share Vehicle History: Providing detailed maintenance and repair records allows your repair shop to diagnose problems efficiently and offer better service.
- Schedule Regular Check-Ins: Establish a routine of monthly or quarterly meetings to review fleet performance, upcoming maintenance schedules, and any recurring issues.
Foster Trust Through Preventative Maintenance
Preventative maintenance is a critical practice that can save your fleet from expensive repairs and unexpected breakdowns. Heavy-duty trucks are complex machines that endure tough conditions. Proactively addressing issues like brake wear, fluid changes, or DOT inspections ensures your fleet stays compliant and operational. Partnering with a repair shop that prioritizes preventative maintenance can help:
- Reduce the frequency of roadside breakdowns.
- Improve fuel efficiency by keeping engines and systems in top condition.
- Extend the lifespan of high-cost components, like turbochargers or differentials.
Insist on Cost Transparency
Money matters are often the biggest friction point between fleet managers and repair shops. To avoid misunderstandings, insist on transparent billing and detailed cost breakdowns. For fleet managers, negotiate a bulk pricing agreement if your fleet requires regular maintenance or frequent repairs. This can lead to significant savings over time. A trustworthy repair shop will:
- Provide Estimates Before Work Begins: Ensure you approve all repairs before parts are ordered or services are performed.
- Offer Itemized Invoices: Look for invoices that clearly separate costs for parts, labor, and any other fees.
- Communicate Cost Overruns Immediately: If unexpected issues arise during a repair, you should be informed and consulted before any additional work begins.
Look for Consistency and Expertise
A dependable repair shop should deliver consistent, high-quality service every time, whether it’s a routine tune-up or an engine overhaul. Consistency builds trust, especially when combined with industry expertise.
How to Evaluate Expertise
- Certifications and Training: Mechanics should have relevant certifications, such as ASE or OEM-specific training.
- Specialization: Ensure the shop has experience working with your fleet’s specific models or configurations, whether they’re long-haul semis or vocational trucks like dump trucks or tankers.
- Diagnostic Accuracy: The shop should use advanced tools like ECM diagnostics or telematics systems to ensure accurate troubleshooting.
Align on Operational Goals
Your repair shop should be more than just a vendor—it should feel like an extension of your own team. Aligning your goals with theirs ensures both parties work towards a shared vision. By maintaining alignment, you’ll ensure that every decision made by the repair shop directly supports your business objectives. For example:
- If uptime is your top priority, your shop should focus on minimizing repair turnaround times.
- If reducing operational costs is your goal, the shop should emphasize preventative care and recommend cost-effective parts.
Leverage Technology for Efficiency
In today’s digital age, a repair shop equipped with cutting-edge technology is indispensable. Modern diagnostic tools and software help mechanics identify and resolve problems quickly, reducing downtime and ensuring optimal vehicle performance. A shop that embraces technology saves you time and money by improving repair accuracy and reducing diagnostic errors. Partnering with a tech-forward shop means fewer surprises and smoother operations. Some common technologies include:
- Telematics Systems: These monitor fleet health remotely, sending alerts for potential issues before they become major repairs.
- ECM Tuning Software: For optimizing fuel efficiency and enhancing engine performance.
- Automated Maintenance Schedulers: To ensure no service intervals are missed.
Choose the Right Partner for Your Fleet Type
Not all repair shops are created equal. Some specialize in over-the-road long-haul fleets, while others focus on vocational trucks used in construction, waste management, or municipal services. Choosing a repair shop familiar with your fleet type ensures better service. Some points to consider when choosing your repair shop include:
- Regulatory Knowledge: Shops that understand industry-specific regulations, like DOT and BIT requirements, can help ensure compliance.
- Parts Availability: A shop with a well-stocked inventory can reduce wait times for repairs.
- Customized Services: For example, a shop serving construction vehicles might offer specialized care for suspensions or drivelines.
Tips for Strengthening the Partnership
Creating a successful long-term partnership with your repair shop requires more than just choosing the right vendor. It’s about nurturing the relationship over time.
Do’s and Don’ts for Building a Partnership
- Do: Schedule annual reviews to assess the shop’s performance and discuss areas for improvement.
- Do: Reward exceptional service by offering repeat business or referrals.
- Don’t: Blame the shop for issues outside their control, like delays due to backordered parts.
By working collaboratively, both parties can thrive.
Establish a Long-Term Vision
Great partnerships don’t happen overnight. Take a long-term approach to your relationship with your repair shop. Over time, this consistency allows your repair partner to learn your fleet’s unique needs, improving both repair quality and efficiency.
Maximize Uptime with Strong Repair Partnerships
Building a strong partnership with a heavy-duty truck fleet repair shop is a strategic investment in your fleet’s longevity and operational success. By prioritizing communication, preventative maintenance, and shared goals, you can create a relationship that drives efficiency and reduces downtime.
Need help finding the right repair partner? Start by looking at Fleetgo Heavy Duty Inc., your shop that values trust, transparency, and a commitment to keeping your fleet rolling. Our team works on fleets and brings your heavy-duty vehicles back in peak condition. Read our article on fleet services to learn more about how to improve fleet performance.
More Articles
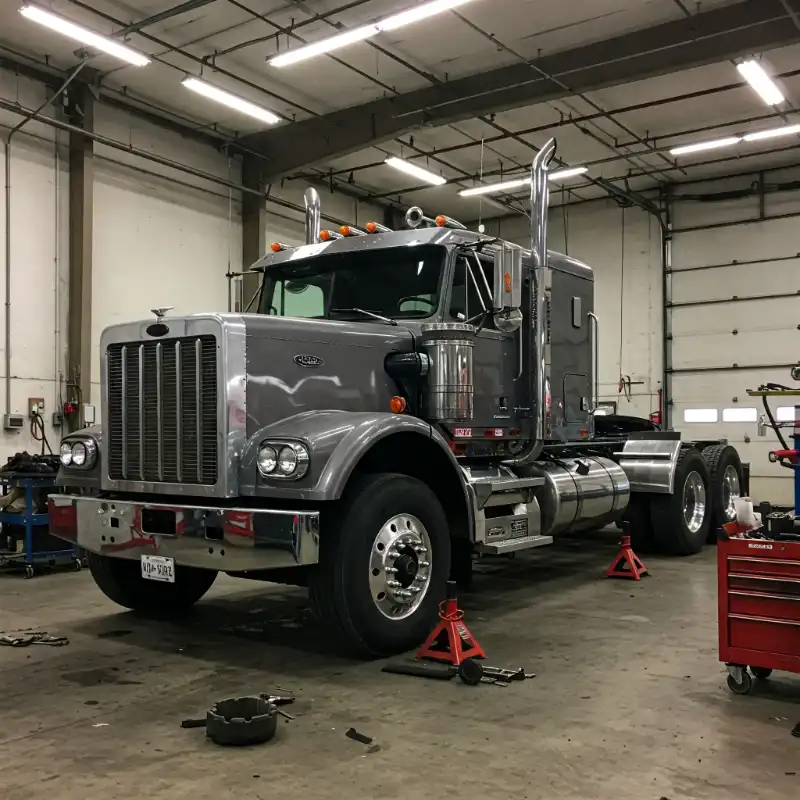
5 Common Issues Found During CVIP Inspections in Edmonton
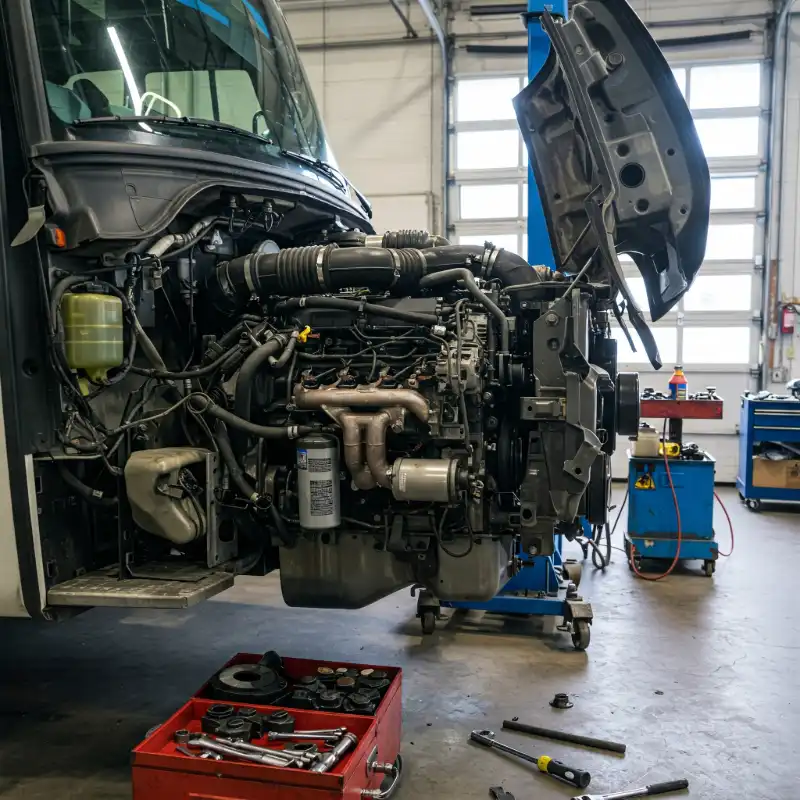
Spring Driving Prep: What Your Car Needs After Winter
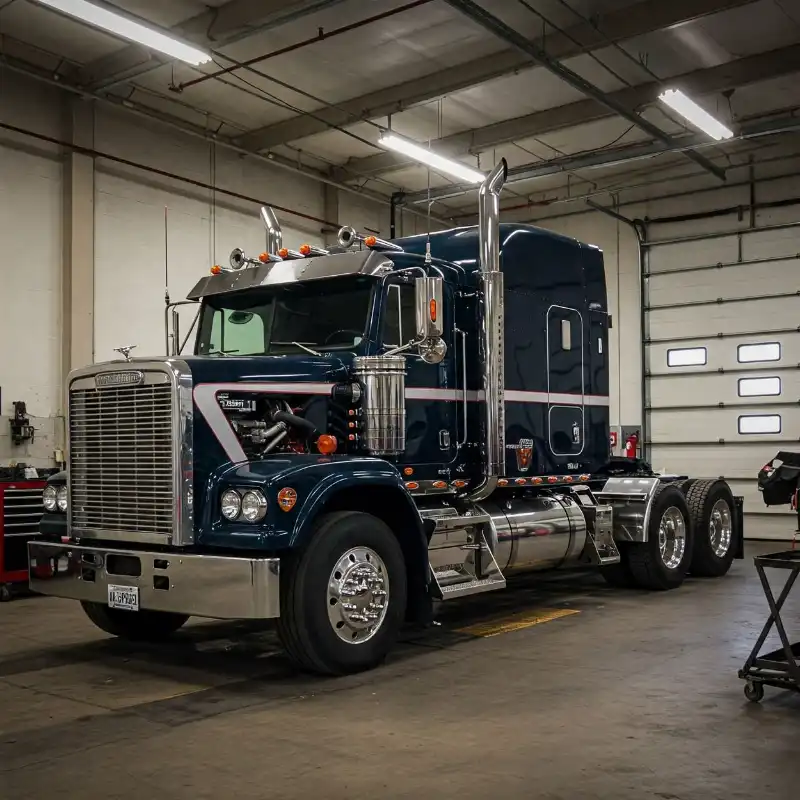
The Biggest Fleet Repair Mistakes Business Owners Make
Contact FleetGo
Get in touch with Fleetgo today to request a quote or to schedule in-shop or mobile services in Edmonton & the surrounding area! Our mobile service extends to a 100km radius around Edmonton for emergency roadside assistance & mobile truck & fleet repairs, including Sherwood Park, Spruce Grove, Fort Saskatchewan, St. Albert, Stony Plain, along Highway 16, & more!
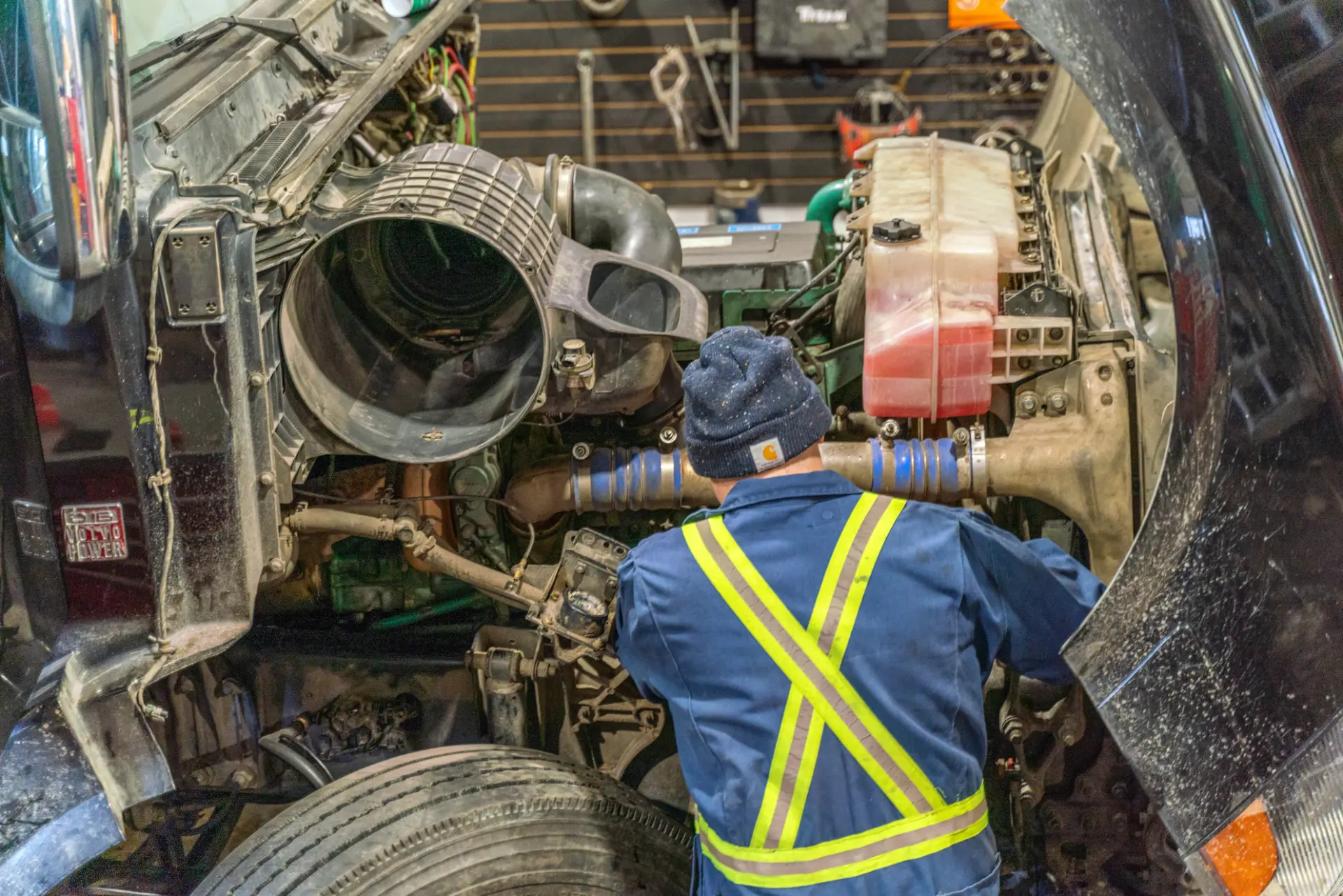