Why Fleet Maintenance Software is Crucial for Optimizing Your Repair Process
Stranded trucks cost you money! Fleet maintenance software streamlines repairs with: data organization, communication tools, scheduling & more. Improve efficiency, save time & money with Fleetgo Heavy Duty.
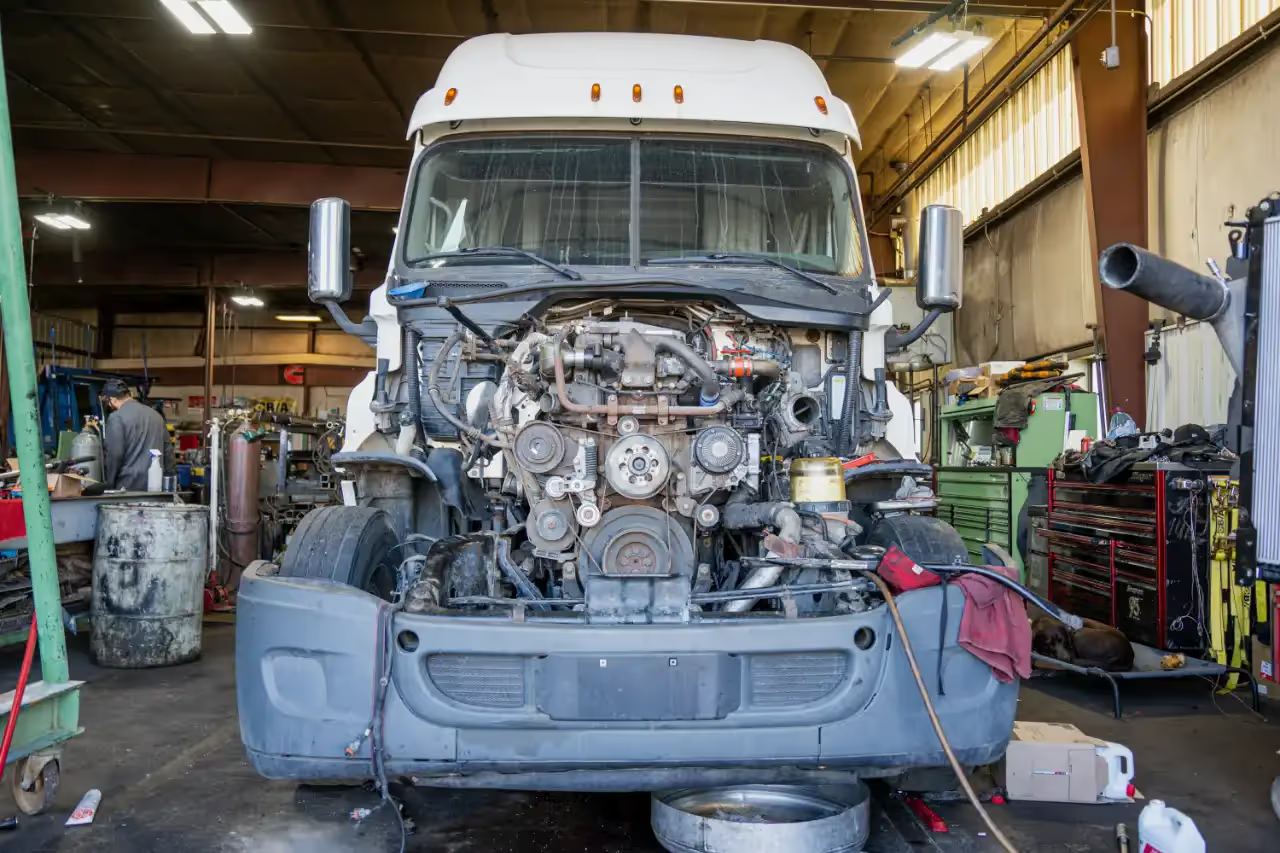
Let’s say a heavy-duty diesel truck breaks down on the side of the highway. What are the consequences? For a fleet manager, it may cause major delays and potential loss of revenue. You scramble to gather information – what type of truck is it? When was its last service? What parts might be needed for the repair? With a paper-based system or outdated software, this process can be time-consuming and frustrating, leading to delays and potentially dissatisfied customers.
Here at Fleetgo Heavy Duty, we understand the challenges faced by fleet managers and repair shops in the heavy-duty truck industry. That's why we're strong advocates for utilizing fleet maintenance software. This article will explore how implementing fleet maintenance software can revolutionize your repair process, optimize efficiency, and ultimately save you time and money.
The Problem with Outdated Repair Processes
Many repair shops still rely on manual systems for managing their fleet service operations. This often involves paper-based records, spreadsheets, and whiteboards. While these methods may have worked in the past, they become increasingly cumbersome and inefficient as your fleet grows or your repair workload increases.
Key Challenges Associated With Outdated Repair Processes
Lost or Inaccessible Information: Crucial details about past repairs, service history, or parts inventory can easily get lost or misplaced in a paper-based system. Locating specific information about a particular heavy-duty truck can be time-consuming, delaying the repair process and potentially causing frustration for both mechanics and clients.
Communication Gaps: Inefficient communication with fleet managers and drivers can lead to misunderstandings and delays. Outdated systems make it difficult to track repair progress, update clients on the status of their vehicles, and ensure everyone is on the same page regarding the repair process.
Inventory Management Issues: Manual inventory tracking can lead to stockouts of essential parts, further delaying repairs. This can result in lost revenue as stranded vehicles wait for parts to become available. Overstocking, on the other hand, can tie up valuable resources unnecessarily, impacting your cash flow.
Inefficient Scheduling: Without a centralized scheduling system, it can be difficult to juggle multiple repair orders, prioritize jobs effectively, and optimize mechanic workloads. This can lead to delays and lost opportunities, as mechanics may be idle while waiting for parts or information, or conversely, overwhelmed with a backlog of jobs.
How Fleet Maintenance Software Streamlines Your Repair Process
Fleet maintenance software offers a comprehensive solution for optimizing your heavy-duty truck repair process. These software programs provide a central hub for managing all aspects of your shop's operations, from work orders and parts inventory to mechanic scheduling and customer communication.
Improved Data Organization and Accessibility
Fleet maintenance software lets you store and access all relevant vehicle information electronically. Service history, repair records, and parts data are readily available at your fingertips, streamlining the repair process and improving decision-making. mechanics can quickly access a vehicle's history to diagnose problems faster and more accurately.
Enhanced Communication
Real-time updates and work order tracking features allow for better communication with fleet managers and drivers. Clients can easily receive updates on repair progress, estimated completion times, and cost estimates through email or mobile apps. This transparency fosters trust and keeps everyone informed throughout the repair process.
Peak Tracking Performance
Get live charts and data about your fleet of heavy-duty trucks. With all the extra information, you can make an informed decision about the next steps. Fleet maintenance management software allows you to understand the vehicles assigned, fuel costs, trends, and more in a simple dashboard. It eases the work and tracks information while also organizing the data you may find useful.
Optimized Scheduling and Workflow
Fleet maintenance software allows you to schedule work orders efficiently, taking into account mechanic availability, parts availability, and repair priorities. This streamlines the workflow, minimizes downtime for vehicles, and maximizes mechanics' productivity. By optimizing the scheduling process, you can ensure your shop is operating at peak efficiency.
Additional Benefits of Fleet Maintenance Software
The benefits of fleet maintenance software extend beyond streamlining your heavy-duty truck repair process. These programs offer a range of features designed to improve the overall efficiency and profitability of your shop:
Improved Preventive Maintenance
Fleet maintenance software facilitates proactive preventive maintenance by scheduling regular service intervals based on manufacturer recommendations or mileage milestones. This helps prevent unexpected breakdowns and costly repairs down the road, maximizing the lifespan and reliability of your client's fleet.
Cost Tracking and Reporting
Detailed reports on labor costs, parts usage, and overall repair costs can be generated. This valuable data allows you to identify areas for cost savings and optimize your pricing structure. You can track trends in parts usage and labor costs to identify potential problems and make informed decisions about parts purchasing and mechanic training.
Improved Customer Service
Fleet maintenance software empowers you to provide a superior customer experience. Real-time updates, transparent communication, and efficient repairs create a more positive experience for your clients, fostering loyalty and repeat business. Automated appointment reminders and online service history access can further enhance the customer experience.
Invest in Efficiency with Fleetgo Heavy Duty
Fleetgo Heavy Duty offers a robust fleet maintenance software solution specifically designed to meet the needs of heavy-duty truck repair shops. We can diagnose and offer help with fleet software to improve your specific workflow. We offer a variety of features to help you manage all aspects of your shop's operations, including:
- Work order creation and tracking
- Parts inventory management
- Mechanic Scheduling
- Customer communication tools
- Preventive maintenance scheduling
- Reporting and analytics
More Articles
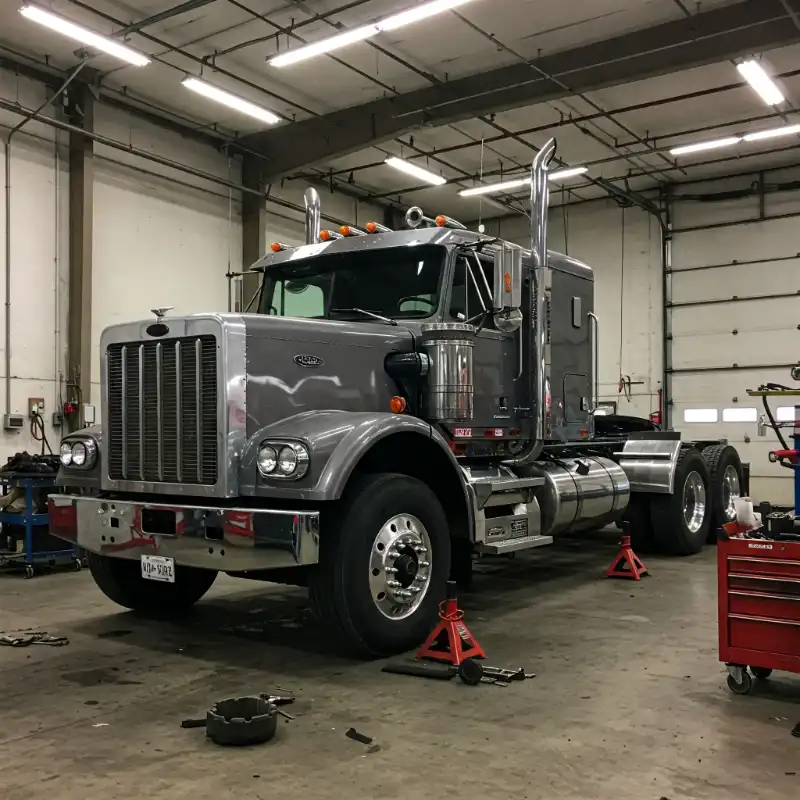
5 Common Issues Found During CVIP Inspections in Edmonton
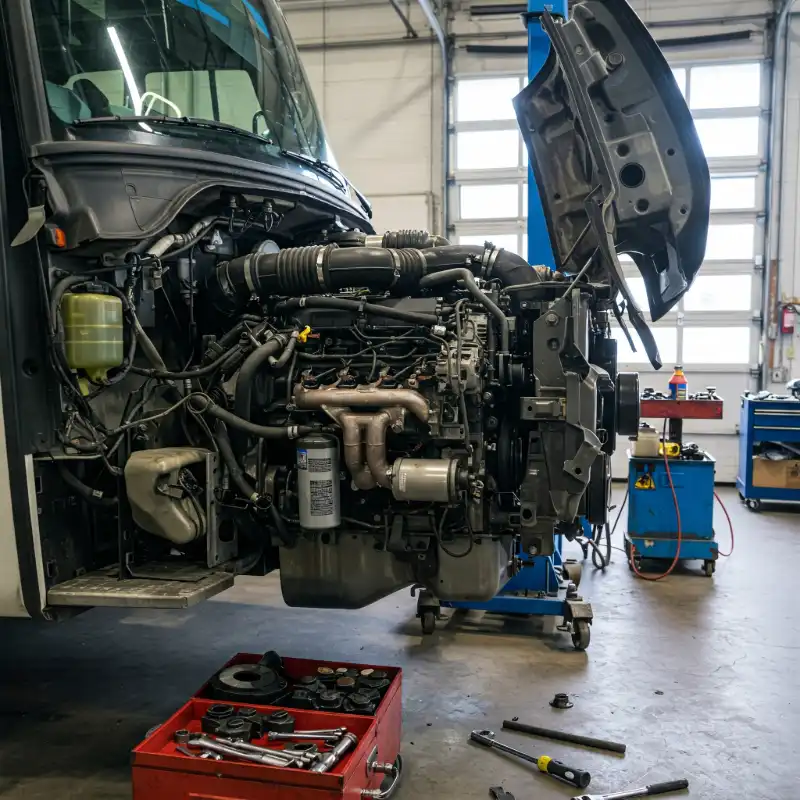
Spring Driving Prep: What Your Car Needs After Winter
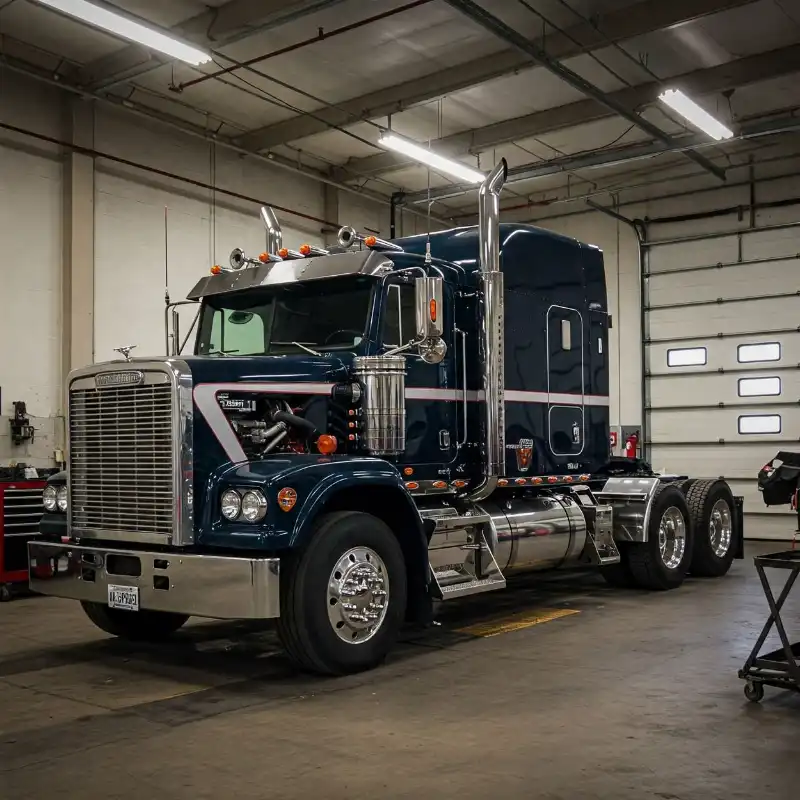
The Biggest Fleet Repair Mistakes Business Owners Make
Contact FleetGo
Get in touch with Fleetgo today to request a quote or to schedule in-shop or mobile services in Edmonton & the surrounding area! Our mobile service extends to a 100km radius around Edmonton for emergency roadside assistance & mobile truck & fleet repairs, including Sherwood Park, Spruce Grove, Fort Saskatchewan, St. Albert, Stony Plain, along Highway 16, & more!
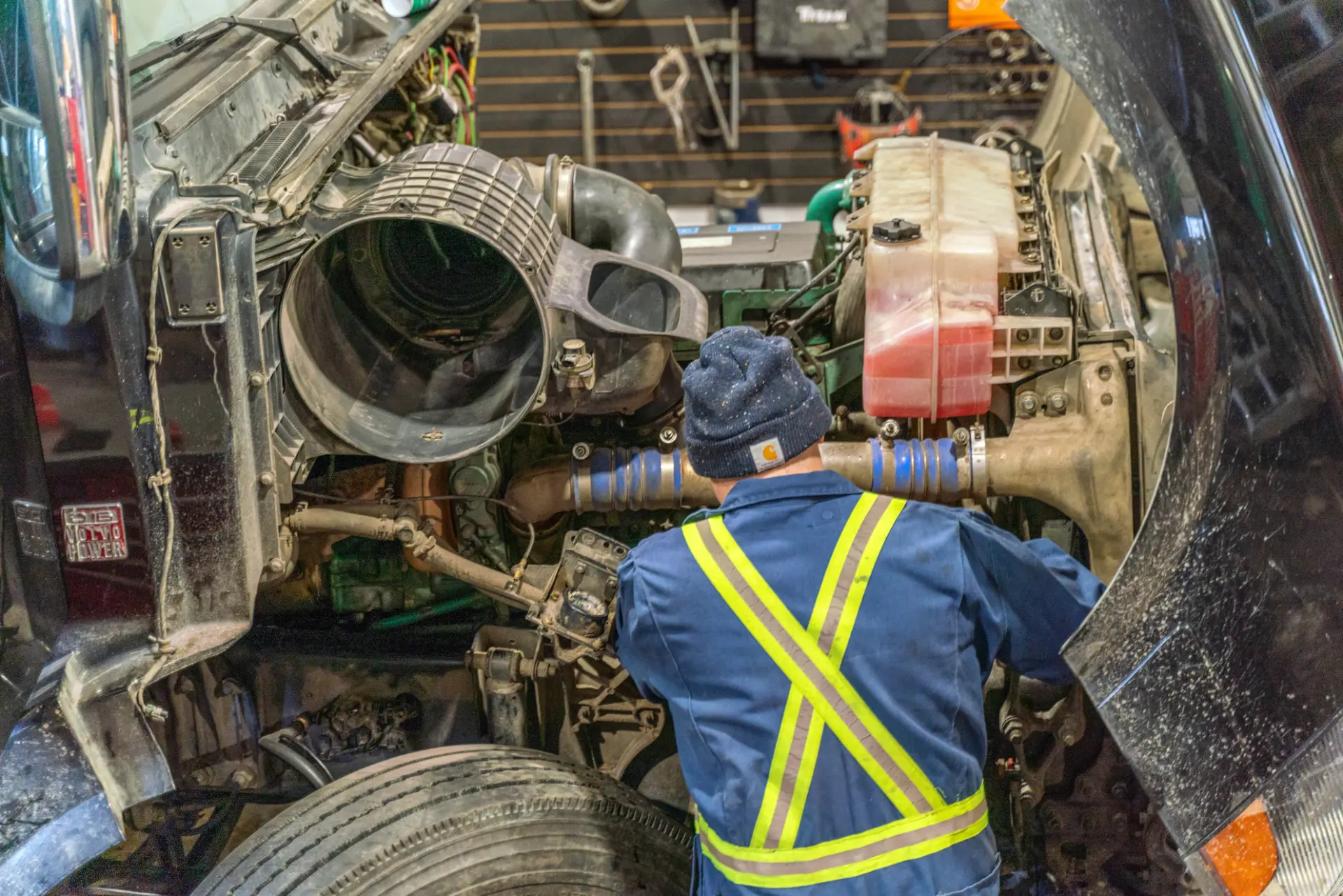